IT IS FINALLY DOWN TO THE CELL (in the complex world of the EV battery cell)
The EV Battery cell is at the heart of EVs that are disrupting the 130 years old Automobile Industry. EV battery cells also happen to be the costliest component of this revolutionary shift.
As global demand and supply for EVs increases, the price of EV Battery Packs keeps on dropping. Between 2010 and 2021 the price of a battery pack has gone down from $1200/kWh to $132/kWh. The battery packs themselves are made up of interconnected modules that are in turn made up of tens to hundreds of rechargeable Li-ion cells that contribute to 77% of the total cost of a battery pack i.e., approximately $101/kWh is the cells cost in a battery pack.
A breakup of cost constitution of a battery cell is given in the following picture:
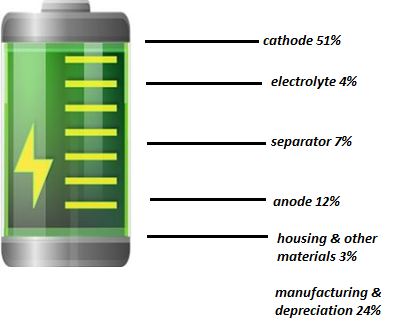
As is evident, cathodes comprise more than half of battery cell cost. The cathode is the positively charged electrode of the battery. When a battery is discharged, both electrons and positively-charged molecules (the eponymous lithium ions) flow from the anode to the cathode, which stores both until the battery is charged again. This means that cathodes effectively determine the performance, range and thermal safety of a battery and therefore of the EV itself, making them one of the most important components. Common cathode compositions are LFP, NMC and NCA – so they typically include lithium and nickel. Battery metals that make up the cathode are in high demand across the globe and currently China is the leading manufacturer of battery cells.
To soften the impact of Chinese dominance in EV battery cells as well as to reduce logistical complications of moving hazardous goods such as batteries, local cell manufacturing is seen as a pragmatic step. Governments and economies around the world have now started creating policies and investing heavily into R&D, innovation and manufacturing of battery cells.
Strides So Far
The European Commission formed the European Battery Alliance (EBA) in 2017 to address the main concerns of self-reliance, a battery cell eco-system for European consumers and a sustainable way of achieving climate neutrality. A total of 38 Gigafactories are being built across Europe to provide a combined output of 1000 gigawatt hours (GWh). The US already has an installed capacity of 43 GWh which currently accounts for 10% of the world’s total installed capacity. Besides lithium-ion technology, US is also seeing private sector investments and start-ups in solid state battery technology as well as silicon-dominant batteries. It is also prioritising mining and processing at home and in its partner countries.
In Asia, apart from China’s dominant position of 77% installed capacity of the world, Japan and Korea are in the 2nd and 3rd position respectively. India is a hub for battery cell minerals like graphite, aluminium, copper, etc. and China imports these minerals from countries like India. India intends migrating from being a minerals supplier to being a materials supplier.
The Indian market is a price-sensitive consumer market. The objectives of India’s National Electric Mobility Mission Plan (NEMMP) will also be easier to achieve with localisation of entire EV supply chain. India has also launched the Phased Manufacturing Programme. This programme plans to support the set-up of few large scale export-competitive integrated batteries cell-manufacturing giga plants in India.
The World Economic Forum (WEF) has proposed setting up a process by G20 nations to handle emerging tensions in the field of electric mobility. WEF has suggested that the EU needs to work more closely with countries with deposits of metals and minerals to improve resource governance.
Why Choose India ?
India has more youth demographically. With rising per capita income, the demand for consumer electronics and EVs have been robust and rising. This makes manufacturing of advanced batteries, creating solutions for battery storage capacity and recycling of batteries, one of the largest economic opportunities of the 21st century in India. There is an abundance of young engineers and scientists in the country that can be utilised towards creating technology solutions. Further, India’s strength in information technologies offers potential to develop intelligent solutions for managing batteries from start to finish.
India’s space agency, ISRO has developed and qualified lithium-ion cells of capacities ranging from 1.5 Ah to 100 Ah for use in satellites and launch vehicles and they have chosen 10 companies for transfer of this technology.
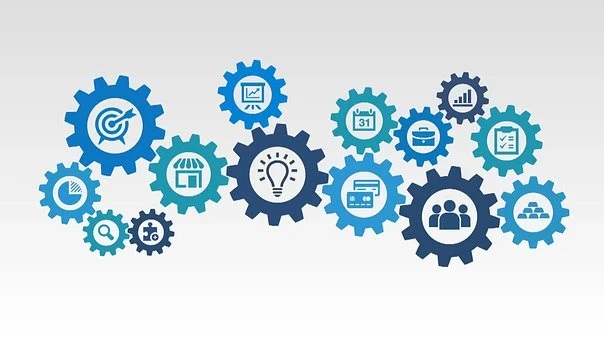
The government has introduced an Auto Production Linked Incentive (PLI) scheme so as to boost the domestic production of futuristic and sophisticated vehicles and components.
As per International Energy Agency’s, India Energy Outlook 2021 projections, India could have 140-200GW of battery storage capacity by the year 2040, potentially a third of total battery storage capacity in the world by then.
Companies on the Front-foot
Major Indian companies are venturing into battery cell manufacturing. Some such companies and their progress till now are given below:
Reliance Industries has plans of investing roughly $7 Bn over three years to offer a fully integrated, end-to-end renewables energy ecosystem, including a factory to manufacture fuel cell technology. Reliance New Energy Solar Ltd. has invested in Ambri Inc., an energy storage company based in Massachusetts, USA. Reliance also has a partnership with BP for energy storage solutions.
Tata Chemicals is also working across the spectrum of lithium-ion technology – from cell manufacturing to recycling used batteries. The company has partnered with reputed R&D centres in India like ISRO, CSIR-CECRI and CMET. The company has already launched battery recycling business.
Incorporated at the prestigious IIT Bombay, Virya Batteries has developed indigenous Lithium-ion cells that offer safety and high cycle life. Virya is backed by Chetan Maini – a serial technopreneur and the mind behind Rewa – India’s first electric car.
Toshiba Corporation, DENSO Corporation, and Suzuki Motor Corporation are establishing TDS Lithium-Ion Battery Gujarat Private Ltd (TDSG) in Gujarat to manufacture and supply Li-ion batteries to Maruti Suzuki and Suzuki Motor Gujarat. “TDSG’s LIB is a very safe rechargeable battery with six exceptional qualities,” according to the official website. Using materials that are based on oxides (Lithium Titanium Oxide), TDS’ LIB is intended to prevent thermal runaway as a result of physical stress-induced short-circuiting.”
Exide Industries and Leclanche SA, one of the world’s leading energy storage firms, have launched a 75:25 joint venture to develop lithium-ion batteries. The cells will be imported from Leclanche’s factory in Germany at first. While cell manufacture will begin at a later date at the local factory, the company’s production line in India is ready to produce Li-ion pouch cell battery modules.
Japanese company Amperex Technology Limited has purchased property in Haryana to build a lithium-ion polymer (LIPO) battery production facility. Larsen & Toubro Power is also working towards developing cell technology.
However, cell manufacturing is still in its nascent stage in India.
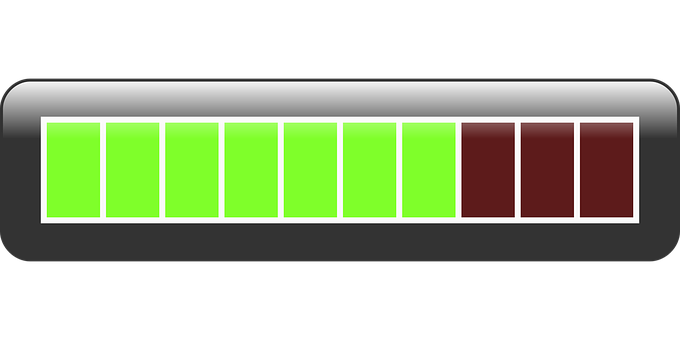
Setting up in India
It is evident that global cell manufacturers as well as Tier 1 and 2 suppliers have a huge opportunity to explore possibilities of JVs and technology transfer agreements. The field has been cleared by government agencies. From research to innovation and from technology transfers to setting up giga factories, the avenues of entry are numerous. India has the strength and IT potential for managing batteries from cradle to grave. This would enable better utilization of batteries in first life applications in EVs as well as potential second life applications in energy storage solutions. Finally, end-of-life waste management directives and extended producer responsibility norms, coupled with recycling efficiency targets, can help the cell manufacturers proactively design and develop circular business models.
However, Indian OEMs must take into account environmental conditions, vehicle specifications and price-sensitive customer segments. LFP is seemingly a better fit for volume segments and commercial applications as per growing consensus. Battery design is crucial for controlling technical specifications and performance parameters as well as to ensure quality and reliability and this can turn out to be a core competitive advantage for OEMs.
For those that have been looking to set up a manufacturing facility, this has been aided by a subsidy, under the PLI Scheme that saw a competitive bidding process. The subsidy is a function of achieved capacity, value addition, actual production and a discounting factor as laid out in the scheme. The scheme aims at incentivising local manufacturing of advanced chemistry cells (ACCs). 75 companies have secured PLI approval under this Component Champion Incentive Scheme. The beneficiaries include big names like Maruti Suzuki, Hero MotoCorp, Tata Autocomp, Mitsubishi Electric, Toyota Kirloskar, Motherson Sumi, Bosch, and Lucas-TVS as well as smaller manufacturers like Neolite ZKW Lightings Private Limited, Vitesco Technologies India Private Limited, . Krishna Landi Renzo India Private Limited and new hitherto non-automotive component investor companies like Bharat Heavy Electricals Limited and Ceat Limited.
There are many other avenues for partnering with Indian cell manufacturers, opportunities in tech R&D tie-ups, innovative and advanced technology solutions, cell design solutions, direct supply of cell components, etc.
India has significant reserves of steel, aluminium, copper, graphite and manganese however, lags in the research and study of potential lithium deposits. Similarly, the demand for recycling capacity better known as Urban Mining is also growing.
A conservative estimate forecasts the size of Indian battery market demand to be $48 billion USD between years 2020-2030.
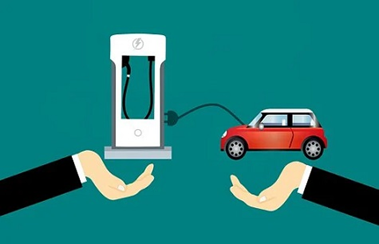
Quanzen and Battery Cell Market Support
Our professionals with over 25 years’ experience in Indian market have supported a number of international suppliers in the Indian market in the area of Electric Mobility.
E-Mobility is growing very fast with huge investments already made in Vehicles, Battery Packs, Powertrain & Controllers. However, Battery Cells manufacturing is comparatively new in the Indian market and we are Specialists in Technical Sales of Products & Solutions “New to Market” in India. We have a deep understanding of the market and established contacts at upcoming Battery Cell makers in India. This helps us ably support International Components and Technical Solutions Supplier Companies in Battery Cell production for an effective India Market Development. We support our Supplier Partners in the complete Sales Cycle from Market Assessment, Entry, Prospecting, Selling & Customer Support.
If you are interested to talk to us about India market opportunity for Battery Cell Supply Chain and how we can help you enter this market and succeed here, do write to me at sudhir.nerurkar@quanzen.com